公差0.03
压制方式高压铸造
加工设备CNC加工中心
加工精度精加工
变形温度360
是否库存是
烧结温度305
加工材料铝合金,铜,不锈钢,钛合金
不锈钢加工具有以下几个显著特点:
### 1. **高硬度与耐磨性**
不锈钢材料通常具有较高的硬度和耐磨性,这使得在加工过程中磨损较快,因此需要使用高硬度、耐磨的材料,如硬质合金或涂层。
### 2. **加工硬化**
不锈钢在加工过程中容易发生加工硬化现象,即材料在切削过程中硬度增加,导致切削力增大,磨损加剧。因此,需要选择合适的切削参数(如切削速度、进给量)以减少加工硬化的影响。
### 3. **导热性差**
不锈钢的导热性较差,导致切削过程中产生的热量不易散发,容易引起工件和温度升高,影响加工精度和寿命。因此,通常需要使用冷却液或润滑剂来降低温度。
### 4. **粘附性强**
不锈钢在加工过程中容易产生切屑粘附现象,切屑容易粘附在表面,影响切削效果和寿命。因此,需要选择适当的几何形状和切削参数来减少粘附。
### 5. **表面质量要求高**
不锈钢产品通常对表面质量要求较高,因此在加工过程中需要严格控制切削参数,避免产生毛刺、划痕等表面缺陷。抛光、研磨等后处理工序也常用于提高表面光洁度。
### 6. **加工难度大**
由于不锈钢的高强度、高硬度和加工硬化等特点,其加工难度相对较大,需要较高的加工技术和设备。数控机床、精密磨床等设备常用于不锈钢加工。
### 7. **多种加工方式**
不锈钢加工可以采用多种方式,包括车削、铣削、钻孔、磨削、冲压、焊接等。不同的加工方式需要根据具体材料和产品要求选择合适的工艺和设备。
### 8. **耐腐蚀性**
不锈钢的耐腐蚀性是其重要特性之一,但在加工过程中需要注意避免引入污染物或破坏其表面保护层,以免影响其耐腐蚀性能。
### 9. **成本较高**
由于不锈钢材料本身成本较高,加上加工难度大、磨损快等因素,不锈钢加工的整体成本相对较高。
### 10. **环保要求**
不锈钢加工过程中产生的废料和冷却液需要妥善处理,以,避免对环境造成污染。
综上所述,不锈钢加工具有高硬度、加工硬化、导热性差等特点,需要选择合适的、切削参数和加工工艺,以确保加工质量和效率。
五轴联动加工是一种的数控加工技术,具有以下特点:
1. **高精度和复杂曲面加工能力**:
五轴联动加工可以同时控制五个坐标轴(X、Y、Z和两个旋转轴),能够实现复杂曲面的高精度加工,适用于、汽车、模具等领域的高精度零件制造。
2. **减少装夹次数**:
传统三轴加工需要多次装夹来加工复杂零件,而五轴联动加工可以在一次装夹中完成多面加工,减少了装夹误差,提高了加工效率和精度。
3. **提高加工效率**:
五轴联动加工可以通过优化路径,减少空行程和加工时间,同时可以使用更短的,提高切削稳定性和加工效率。
4. **的表面质量**:
五轴联动加工可以保持与工件表面的角度,减少振动和切削力,从而获得的表面光洁度和加工质量。
5. **加工灵活性高**:
五轴联动加工可以处理复杂几何形状的零件,包括深腔、窄缝、倒扣等传统加工难以完成的部位。
6. **减少磨损**:
通过优化角度和切削路径,五轴联动加工可以延长寿命,降低加工成本。
7. **应用范围广**:
五轴联动加工适用于多种材料,包括金属、复合材料、塑料等,广泛应用于、器械、能源设备、模具制造等行业。
8. **技术要求高**:
五轴联动加工对机床、编程和操作人员的技术要求较高,需要复杂的编程和的机床控制。
总之,五轴联动加工是一种、高精度的加工技术,特别适合复杂零件的制造,能够显著提高生产效率和产品质量。
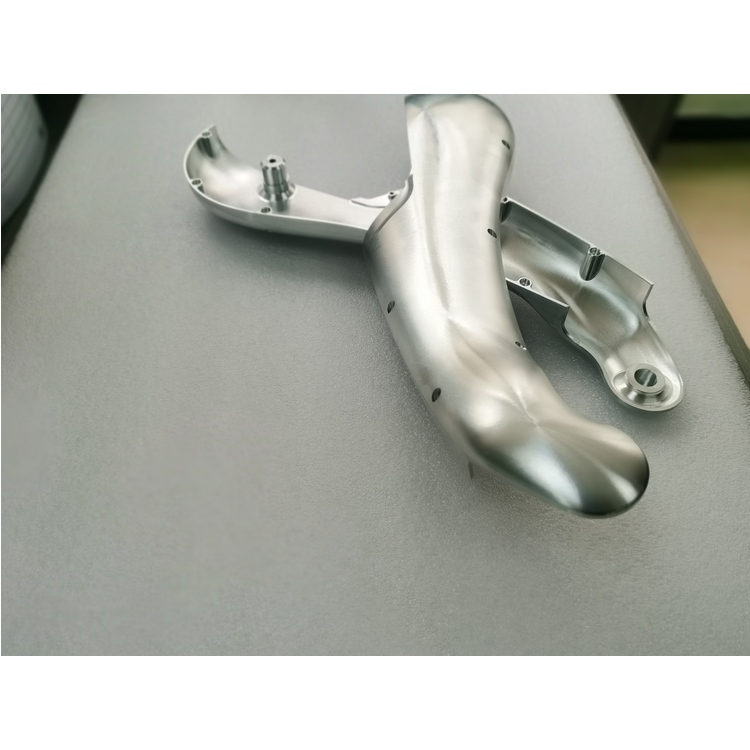
电器外壳加工的特点主要体现在以下几个方面:
1. **材料多样性**:
电器外壳的材料种类繁多,常见的有塑料、金属(如铝合金、不锈钢、镀锌钢板等)、复合材料等。不同材料的选择取决于电器产品的应用场景、功能需求和成本考虑。
2. **加工工艺复杂**:
电器外壳的加工涉及多种工艺,包括注塑成型(塑料外壳)、冲压成型(金属外壳)、CNC加工、压铸、折弯、焊接、表面处理(如喷涂、电镀、阳氧化等)等。每种工艺都有其特定的技术要求和流程。
3. **精度要求高**:
电器外壳需要与内部组件配合,因此对尺寸精度、形状精度和表面质量的要求较高。特别是在安装孔、接口位置、按键孔等关键部位,加工精度直接影响产品的装配和使用性能。
4. **表面处理要求严格**:
电器外壳的表面处理不仅影响产品的外观美观度,还涉及防腐蚀、耐磨、绝缘等功能性需求。常见的表面处理工艺包括喷涂、电镀、阳氧化、拉丝、抛光等,具体选择取决于材料和产品要求。
5. **功能性与美观性并重**:
电器外壳不仅是保护内部组件的结构件,也是产品外观设计的重要组成部分。加工时需要兼顾功能性(如散热、防水、防尘等)和美观性(如线条设计、颜色搭配、质感等)。
6. **定制化程度高**:
不同电器产品的需求差异较大,外壳的设计和加工往往需要根据具体产品进行定制。定制化加工包括形状、尺寸、材料、表面处理等方面的个性化设计。
7. **生产效率与成本控制**:
电器外壳加工通常需要大批量生产,因此生产效率和成本控制是关键。采用自动化生产线、优化工艺流程、减少材料浪费等措施可以提率并降。
8. **环保与安全性**:
电器外壳的材料和加工工艺需要,特别是塑料材料的选择和表面处理工艺应避免使用有害物质。此外,外壳的加工还需要确保产品的安全性,如防火、防触电等。
9. **散热与电磁屏蔽设计**:
部分电器外壳需要具备良好的散热性能或电磁屏蔽功能,加工时需考虑散热孔、散热片的设计,以及金属材料的电磁屏蔽效果。
10. **质量控制严格**:
电器外壳的质量直接影响产品的整体性能和用户体验,因此加工过程中需要严格的质量控制,包括尺寸检测、表面质量检查、功能测试等。
综上所述,电器外壳加工是一个多工艺、多材料、高精度、定制化的过程,需要综合考虑功能性、美观性、生产效率和成本控制等多方面因素。
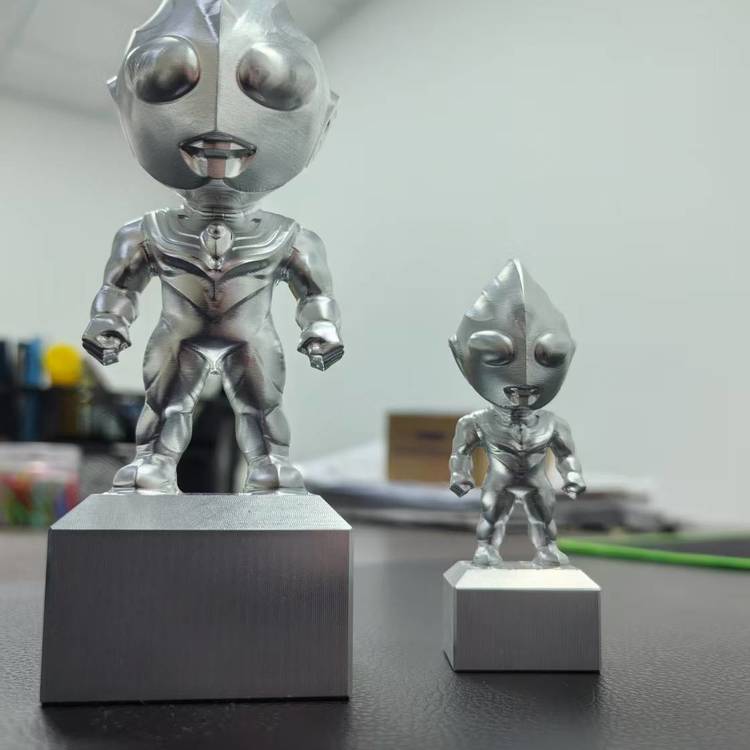
机械零件加工的特点主要包括以下几个方面:
### 1. **高精度要求**
- 机械零件加工通常对尺寸精度、形状精度和位置精度有严格要求,以确保零件在装配和使用过程中能够达到预期的性能。
- 加工精度通常以微米(μm)为单位,某些高精度零件甚至要求达到纳米级别。
### 2. **多样化的加工方法**
- 机械零件加工涉及多种加工方法,如车削、铣削、磨削、钻削、镗削、拉削、冲压、铸造、锻造等。
- 根据零件的材料、形状和精度要求,选择合适的加工工艺。
### 3. **材料种类广泛**
- 机械零件加工涉及的材料种类繁多,包括金属(如钢、铝、铜、钛等)、合金、塑料、陶瓷、复合材料等。
- 不同材料的加工性能和工艺参数差异较大,需要根据材料特性调整加工方法。
### 4. **复杂的几何形状**
- 机械零件的形状多样,包括轴类、盘类、箱体类、异形件等。
- 加工过程中需要处理复杂的几何特征,如曲面、螺纹、孔、槽、齿轮等。
### 5. **批量生产与单件生产并存**
- 机械零件加工既包括大批量生产(如汽车零部件、标准件),也包括单件或小批量生产(如定制设备、模具)。
- 批量生产通常采用自动化设备和流水线作业,而单件生产则更注重灵活性和定制化。
### 6. **设备与工具的高要求**
- 机械零件加工需要高精度、率的加工设备,如数控机床(CNC)、加工中心、磨床等。
- 加工的选择和磨损控制对加工质量和效率有重要影响。
### 7. **工艺链长**
- 机械零件的加工通常需要经过多道工序,如毛坯制备、粗加工、半精加工、精加工、热处理、表面处理等。
- 各工序之间需要紧密配合,以确保终零件的质量和性能。
### 8. **严格的质量控制**
- 机械零件加工过程中需要进行严格的质量检测,包括尺寸测量、表面粗糙度检测、硬度测试、无损检测等。
- 质量控制贯穿于整个加工过程,以确保零件符合设计要求和标准。
### 9. **成本与效率的平衡**
- 机械零件加工需要在的前提下,尽可能降和提率。
- 通过优化工艺、采用设备和技术、提高自动化程度等方式,实现成本与效率的平衡。
### 10. **环境与安全要求**
- 机械零件加工过程中会产生切屑、粉尘、噪音、振动等,需要采取环保措施,如切屑回收、除尘、降噪等。
- 操作人员需要遵守安全操作规程,佩戴防护装备,以防止事故的发生。
### 11. **技术更新快**
- 机械零件加工技术不断发展,如数控技术、增材制造(3D打印)、智能制造、绿色制造等新技术的应用,提高了加工精度、效率和环保性。
- 企业需要不新设备和技术,以适应市场需求和技术进步。
### 12. **定制化与标准化结合**
- 机械零件加工既需要满足标准化生产的要求,也需要根据客户需求进行定制化设计。
- 标准化零件可以通过大规模生产降,而定制化零件则能够满足特定应用场景的需求。
总之,机械零件加工是一个复杂且技术要求高的领域,涉及多方面的知识和技能,需要综合考虑材料、工艺、设备、质量、成本等因素,以实现、量的加工目标。
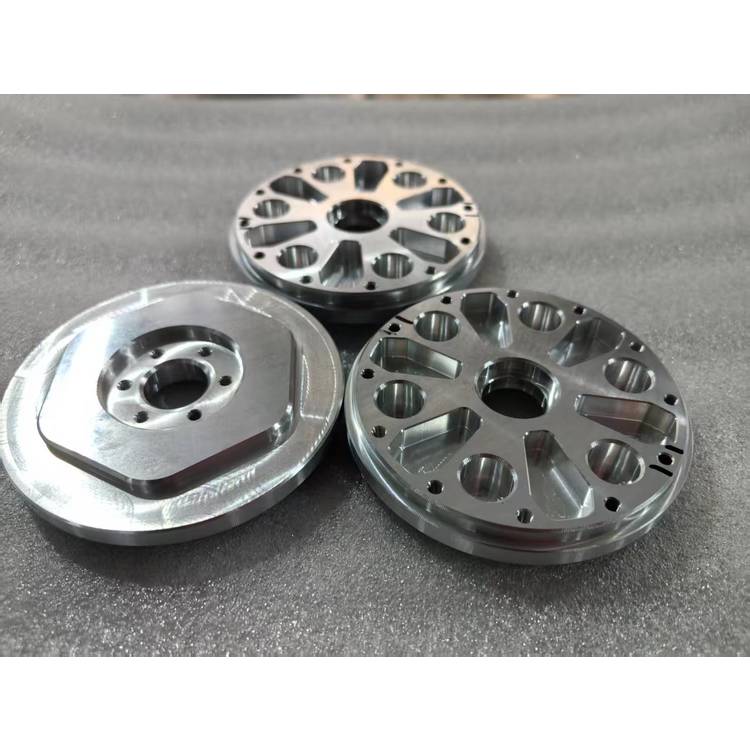
数控车床(Computer Numerical Control Lathe)是一种通过计算机程序控制加工过程的机床,具有高精度、率、高自动化等特点。以下是数控车床加工的主要特点:
### 1. **高精度与高重复性**
- 数控车床通过计算机程序控制的运动轨迹,能够实现微米级甚至更高精度的加工。
- 由于加工过程由程序控制,重复加工时能够保持高度一致,适合大批量生产。
### 2. **加工复杂形状能力强**
- 数控车床可以加工复杂的三维曲面、螺纹、锥面等形状,传统车床难以实现的复杂工件可以通过数控车床轻松完成。
- 通过多轴联动功能,可以实现更复杂的加工任务。
### 3. **自动化程度高**
- 数控车床可以自动完成从毛坯到成品的整个加工过程,减少了人工干预。
- 配备自动换刀装置(如刀塔)和自动上下料系统后,可以实现连续加工,进一步提率。
### 4. **加工效率高**
- 数控车床的切削速度和进给量可以控制,优化加工参数后能够显著提高加工效率。
- 减少了传统车床中手动调整和测量的时间,缩短了加工周期。
### 5. **灵活性高**
- 通过修改加工程序,可以快速适应不同工件的加工需求,特别适合多品种、小批量生产。
- 加工参数(如转速、进给量、切削深度等)可以根据工件材料和形状灵活调整。
### 6. **减少人为误差**
- 加工过程由程序控制,减少了操作人员的技术水平和经验对加工质量的影响。
- 降低了因人为操作失误导致的废品率。
### 7. **集成化与智能化**
- 现代数控车床通常配备智能化功能,如自动检测、磨损补偿、加工误差修正等,进一步提高了加工质量和效率。
- 可以与CAD/CAM系统无缝集成,实现从设计到加工的一体化流程。
### 8. **适用范围广**
- 数控车床可以加工材料,包括金属、塑料、复合材料等。
- 适用于多种行业,如、汽车制造、模具加工、器械等。
### 9. **减少工装夹具需求**
- 数控车床可以通过程序控制实现复杂形状的加工,减少了对工装夹具的依赖,降低了生产成本。
### 10. **环保与节能**
- 数控车床的加工过程更加,减少了材料浪费。
- 现代数控车床通常配备节能技术,降低了能源消耗。
### 总结
数控车床加工以其高精度、率、高自动化和灵活性的特点,在现代制造业中占据了重要地位。它不仅适用于大批量生产,也能满足多品种、小批量的加工需求,是提升生产效率和产品质量的重要工具。
非标王金件加工,通常指的是非标准、定制化的金属零件加工,其特点主要体现在以下几个方面:
### 1. **高度定制化**
- 非标王金件加工是根据客户的具体需求进行设计和生产的,通常没有现成的标准规格可供参考,因此需要根据客户提供的图纸或要求进行定制化加工。
### 2. **复杂的工艺要求**
- 由于是非标准件,加工过程中可能需要采用多种工艺,如车削、铣削、磨削、钻孔、焊接、热处理等,工艺复杂且技术要求较高。
### 3. **高精度要求**
- 非标王金件通常用于精密设备或特殊场合,因此对尺寸精度、表面光洁度、形位公差等有较高要求,加工过程中需要严格控制质量。
### 4. **材料多样性**
- 非标王金件加工可能涉及多种金属材料,如不锈钢、铝合金、铜合金、钛合金等,不同材料的加工性能和工艺要求各不相同。
### 5. **小批量生产**
- 非标件通常是按需定制,生产批量较小,甚至可能是单件生产,因此生产成本相对较高。
### 6. **灵活性强**
- 加工过程中需要根据实际情况灵活调整工艺和设备,以适应不同的形状、尺寸和材料要求。
### 7. **交货周期较长**
- 由于需要定制设计和加工,非标王金件的生产周期通常比标准件更长,尤其是对于复杂零件,可能需要多次试制和调整。
### 8. **成本较高**
- 非标件加工涉及定制设计、复杂工艺和小批量生产,因此单位成本通常高于标准件。
### 9. **质量检测严格**
- 由于非标件通常用于关键部位,质量检测要求严格,可能需要使用三坐标测量仪、投影仪等精密检测设备。
### 10. **技术要求高**
- 加工非标王金件需要具备丰富的经验和的技术,包括对材料性能、加工工艺、设备操作等方面的深入理解。
### 应用领域
非标王金件广泛应用于、汽车制造、器械、电子设备、模具制造等高精度、高技术要求的行业。
总之,非标王金件加工是一项技术含量高、工艺复杂、灵活性强的定制化服务,需要具备的技术和设备支持。
http://www.hfmaiqi.com