公差0.03
压制方式高压铸造
加工设备CNC加工中心
加工精度精加工
变形温度360
是否库存是
烧结温度305
加工材料铝合金,铜,不锈钢,钛合金
CNC加工(Computer Numerical Control,计算机数控加工)是一种利用计算机控制的精密加工技术,具有以下特点:
### 1. **高精度**
- CNC加工能够实现高的加工精度,通常可达到微米级别的精度,适用于对尺寸要求严格的零件制造。
### 2. **率**
- CNC机床可以连续工作,自动化程度高,减少了人工干预,提高了生产效率。
- 通过编程可以实现复杂形状的快速加工,缩短了生产周期。
### 3. **灵活性**
- 只需修改程序即可加工不同形状和尺寸的零件,适应多品种、小批量生产的需求。
- 适用于多种材料,如金属、塑料、木材、复合材料等。
### 4. **复杂形状加工能力**
- CNC加工可以完成传统加工难以实现的复杂几何形状,如曲面、三维轮廓等。
- 支持多轴联动(如3轴、4轴、5轴加工),进一步扩展了加工范围。
### 5. **一致性好**
- 由于加工过程由计算机控制,避免了人为误差,保证了批量生产时零件的一致性和稳定性。
### 6. **减少材料浪费**
- CNC加工通过的编程和路径优化,大限度地减少材料浪费,降。
### 7. **自动化程度高**
- CNC机床可以集成自动换刀、自动测量等功能,实现无人值守或半自动化生产。
### 8. **可重复性**
- 加工程序可以保存并重复使用,确保相同零件的加工结果一致。
### 9. **适用范围广**
- 适用于多种行业,如、汽车制造、模具制造、器械、电子产品等。
### 10. **减少人力需求**
- 操作人员只需掌握编程和机床操作技能,减少了传统加工中对熟练工人的依赖。
### 11. **支持多种加工方式**
- CNC技术可用于铣削、车削、钻孔、磨削、线切割等多种加工方式。
### 12. **易于集成**
- CNC机床可以与其他自动化设备(如机器人、传送带)集成,形成智能制造系统。
### 13. **成本较高**
- CNC设备和编程技术的初期投入较高,但长期来看,其效率和精度可以降低综合成本。
### 14. **对操作人员要求高**
- 需要操作人员具备一定的编程和机械加工知识,同时对设备的维护和保养要求较高。
### 总结
CNC加工以其高精度、率、灵活性和自动化等优势,成为现代制造业中的技术,特别适用于复杂零件和高精度产品的制造。
陶瓷焊接加工是一种用于连接陶瓷材料的特殊工艺,具有以下特点:
### 1. **高难度性**
- 陶瓷材料通常具有高硬度、脆性和低延展性,焊接过程中容易产生裂纹或断裂,因此对工艺要求高。
### 2. **高温需求**
- 陶瓷的熔点通常较高,焊接时需要高温环境,有时甚至需要借助激光、电子束等技术来实现。
### 3. **特殊焊接方法**
- 常用的陶瓷焊接方法包括:
- **扩散焊接**:通过高温和压力使陶瓷表面原子扩散形成连接。
- **活性金属钎焊**:使用活性钎料(如钛、锆等)改善陶瓷与金属或陶瓷之间的润湿性。
- **激光焊接**:利用高能激光束实现局部加热和熔化。
- **超声波焊接**:通过超声波振动产生热量实现连接。
### 4. **材料匹配性要求高**
- 陶瓷与金属或其他陶瓷的焊接需要材料的热膨胀系数、化学相容性等性能相匹配,否则容易产生应力或失效。
### 5. **接头质量关键**
- 焊接接头的强度、气密性和耐腐蚀性是衡量焊接质量的重要指标,需要严格控制工艺参数。
### 6. **应用领域广泛**
- 陶瓷焊接加工广泛应用于、电子、器械、能源等领域,如陶瓷基复合材料、高温传感器、燃料电池等。
### 7. **设备和技术要求高**
- 需要高精度的设备和的技术支持,如真空环境、的温度控制和压力控制等。
### 8. **成本较高**
- 由于工艺复杂、设备昂贵,陶瓷焊接加工的成本通常较高。
总之,陶瓷焊接加工是一项技术密集型工艺,需要综合考虑材料特性、工艺方法和应用需求,以实现量的连接效果。
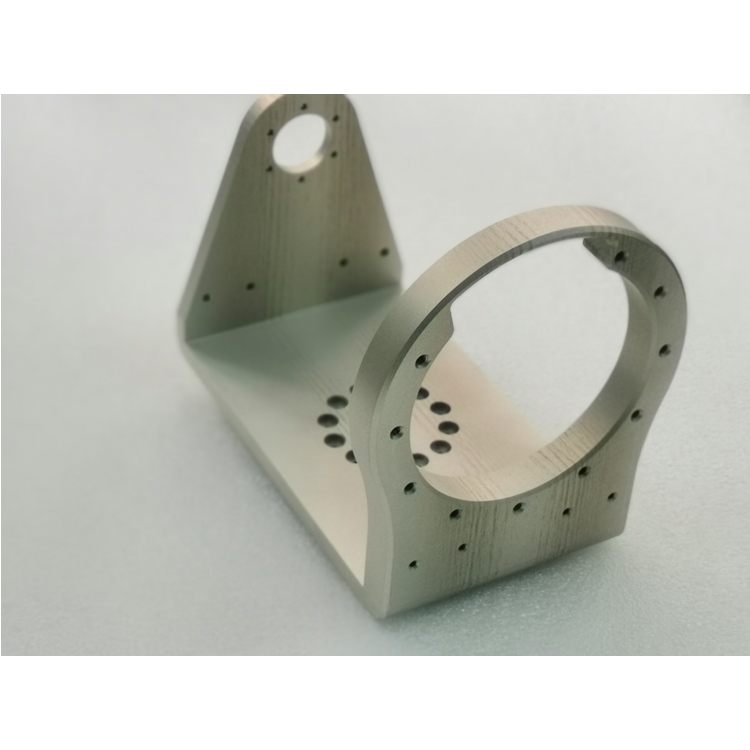
四轴零件加工是一种在数控机床(CNC)上进行的高精度加工技术,它利用四个运动轴(通常是X、Y、Z轴和一个旋转轴)来完成复杂零件的加工。以下是四轴零件加工的主要特点:
### 1. **复杂几何形状的加工能力**
- 四轴加工可以通过旋转轴(通常是A轴或B轴)实现工件的多角度加工,能够处理复杂的几何形状,如曲面、倾斜面、螺旋槽等。
- 相比三轴加工,四轴加工减少了工件的装夹次数,提高了加工效率和精度。
### 2. **减少装夹次数**
- 四轴加工可以通过旋转轴调整工件的位置,无需多次拆卸和重新装夹,从而减少加工时间,降低误差累积。
- 特别适用于需要多面加工的零件,如叶轮、凸轮、模具等。
### 3. **提高加工精度**
- 由于减少了装夹次数,四轴加工能够地保持工件的加工基准,从而提高整体加工精度。
- 旋转轴的加入使得能够以更合适的角度接近工件,减少干涉,提高表面质量。
### 4. **适用于复杂零件**
- 四轴加工特别适合加工复杂零件,如零件、器械、汽车零部件等,这些零件通常具有复杂的曲面和多角度特征。
### 5. **灵活性和效率**
- 四轴加工可以在一次装夹中完成多面加工,减少了加工工序,提高了生产效率。
- 对于需要多次换刀或调整角度的加工任务,四轴加工更具灵活性。
### 6. **降**
- 由于减少了装夹次数和加工时间,四轴加工可以降低人工成本和加工成本。
- 对于批量生产复杂零件,四轴加工的经济性更为明显。
### 7. **技术要求较高**
- 四轴加工需要更高的编程技术,尤其是对旋转轴的控制和路径的优化。
- 操作人员需要具备较高的数控编程和加工经验,以确保加工精度和效率。
### 8. **适用范围广**
- 四轴加工适用于多种材料,包括金属(如铝、钢、钛合金)、塑料、复合材料等。
- 广泛应用于、汽车制造、模具制造、器械等行业。
### 9. **与五轴加工的区别**
- 相比五轴加工,四轴加工缺少一个旋转轴,因此在加工某些其复杂的零件时可能受到限制。
- 然而,四轴加工在成本和技术门槛上更具优势,适合大多数复杂零件的加工需求。
### 总结
四轴零件加工以其高精度、率和多角度加工能力,成为复杂零件制造的重要技术。它在减少装夹次数、提高加工灵活性和降方面具有显著优势,广泛应用于多个工业领域。

机床零件加工的特点主要包括以下几个方面:
1. **高精度要求**:机床零件的加工精度直接影响机床的整体性能和使用寿命。因此,在加工过程中,需要严格控制尺寸公差、形位公差和表面粗糙度,以确保零件的精度和一致性。
2. **复杂几何形状**:机床零件通常具有复杂的几何形状,如曲面、孔、槽、螺纹等。这要求加工设备具备多轴联动功能,能够实现复杂轮廓的加工。
3. **材料多样性**:机床零件可能使用多种材料,包括铸铁、钢、铝合金、铜合金等。不同材料的加工性能各异,需要选择合适的、切削参数和加工工艺。
4. **高强度与耐磨性**:机床零件通常需要承受较大的载荷和摩擦力,因此要求材料具有较高的强度和耐磨性。加工过程中需要保证零件的机械性能和表面硬度。
5. **批量生产与单件定制**:机床零件的生产既有批量化的标准件,也有根据客户需求定制的非标件。批量生产时要求、稳定的加工工艺,而定制件则需要灵活的生产能力和快速响应。
6. **加工工艺复杂**:机床零件的加工通常涉及多种工艺,如车削、铣削、磨削、钻孔、镗孔、热处理等。这些工艺需要合理安排,以确保零件的加工质量和效率。
7. **高表面质量**:机床零件的表面质量对机床的运行平稳性和使用寿命有重要影响。因此,在加工过程中需要采用精细的切削工艺和表面处理技术,以获得良好的表面光洁度和耐磨性。
8. **严格的检测与质量控制**:机床零件的加工过程中需要进行严格的质量控制和检测,包括尺寸测量、形位公差检测、表面粗糙度检测等,以确保零件符合设计要求。
9. **自动化与智能化**:随着工业4.0的发展,机床零件加工越来越多地采用自动化和智能化技术,如数控机床、机器人、自动检测系统等,以提高生产效率和加工精度。
10. **环保与节能**:现代机床零件加工越来越注重环保和节能,采用绿色制造技术,减少资源消耗和环境污染。
综上所述,机床零件加工具有高精度、复杂形状、材料多样、高强度、复杂工艺等特点,要求加工设备和技术具备高度的灵活性和性。
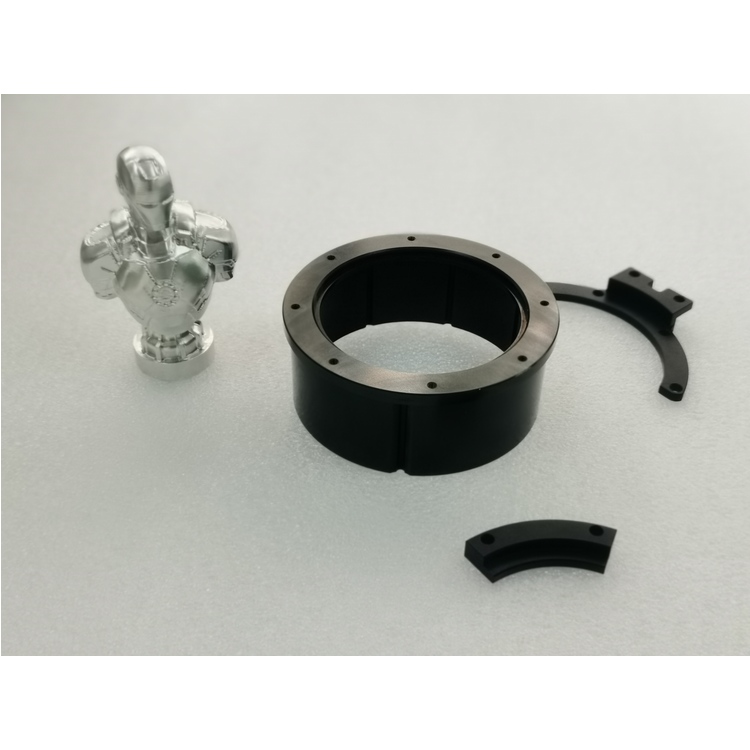
车铣复合加工是一种集成了车削和铣削功能的制造技术,具有以下特点:
### 1. **高度集成**
- **多功能性**:车铣复合加工中心可以在一台设备上完成车削、铣削、钻孔、攻丝等多种加工工序,减少了设备数量和占地面积。
- **工序集中**:通过一次装夹完成多道工序,减少工件在不同设备间的搬运和重新装夹,提高加工效率。
### 2. **高精度**
- **减少装夹误差**:由于工件只需一次装夹,避免了多次装夹带来的定位误差,提高了加工精度。
- **动态补偿**:现代车铣复合加工中心通常配备高精度传感器和控制系统,能够实时监测和补偿加工误差。
### 3. **率**
- **缩短加工时间**:通过工序集中和自动化操作,显著缩短了加工周期。
- **自动化程度高**:配备自动换刀系统、自动上下料装置等,减少人工干预,提高生产效率。
### 4. **复杂零件加工能力**
- **多轴联动**:车铣复合加工中心通常具有多轴(如5轴、7轴等)联动功能,能够加工复杂的三维曲面和异形零件。
- **灵活性强**:能够处理复杂几何形状的工件,适用于、汽车、模具等高精度制造领域。
### 5. **节约成本**
- **减少设备投资**:一台车铣复合加工中心可以替代多台传统机床,降低了设备采购和维护成本。
- **降低人工成本**:自动化程度高,减少了操作人员数量和劳动强度。
### 6. **提高加工质量**
- **表面质量好**:通过优化加工路径和参数,可以获得的表面光洁度和尺寸精度。
- **减少变形**:由于减少了装夹次数和加工应力,工件变形和残余应力得到有效控制。
### 7. **适应性强**
- **材料广泛**:适用于金属材料(如钢、铝、钛合金等)以及非金属材料的加工。
- **批量生产与单件生产**:既适合大批量生产,也适合小批量、多品种的柔性生产。
### 8. **技术**
- **智能化**:集成的数控系统、CAD/CAM软件和在线检测技术,实现智能化加工。
- **绿色制造**:通过优化加工工艺,减少材料浪费和能源消耗,符合绿色制造理念。
### 总结
车铣复合加工技术通过集成多种加工功能,显著提高了加工效率、精度和灵活性,特别适用于复杂零件的高精度制造。它在现代制造业中具有广泛的应用前景,能够有效降低生产成本,提高产品质量。
数控机床(Computer Numerical Control, CNC)机加工是一种高精度、率的制造技术,具有以下特点:
### 1. **高精度**
- 数控机床通过计算机程序控制,能够实现微米级甚至更高精度的加工,确保工件的尺寸和形状符合设计要求。
### 2. **高自动化**
- 数控机床可以自动完成复杂的加工任务,减少人工干预,降低人为误差,提高生产效率。
### 3. **高灵活性**
- 通过更换程序,数控机床可以快速适应不同工件的加工需求,适用于多品种、小批量生产。
### 4. **复杂形状加工**
- 数控机床能够完成传统机床难以实现的复杂几何形状加工,如曲面、螺旋槽等。
### 5. **一致性好**
- 数控加工通过程序控制,确保批量生产中每个工件的加工质量和尺寸一致性。
### 6. **生产效率高**
- 数控机床可以连续工作,减少换刀、调整等非加工时间,同时支持多轴联动,进一步提高加工效率。
### 7. **减少人为误差**
- 由于加工过程由程序控制,减少了操作工人的技术依赖,降低了人为因素导致的误差。
### 8. **易于修改和优化**
- 加工程序可以随时修改和优化,适应设计变更或工艺改进,灵活性高。
### 9. **多功能性**
- 现代数控机床通常集成了多种加工功能,如车削、铣削、钻孔、磨削等,实现一机多用。
### 10. **减少材料浪费**
- 数控机床通过控制,减少了材料浪费,特别适用于高价值材料的加工。
### 11. **降低劳动强度**
- 操作人员只需监控和调整程序,劳动强度较低,工作环境相对安全。
### 12. **支持数字化管理**
- 数控机床可以与计算机设计(CAD)和计算机制造(CAM)系统无缝对接,实现数字化生产管理。
### 13. **高初始投资**
- 数控机床的设备成本和维护成本较高,但长期来看,其率和量可以带来显著的经济效益。
### 14. **对操作人员要求高**
- 需要操作人员具备一定的编程和调试能力,以及对数控系统的深入理解。
### 15. **适应性强**
- 数控机床可以加工多种材料,包括金属、塑料、复合材料等,应用范围广泛。
总之,数控机床机加工以其高精度、率和灵活性,在现代制造业中占据重要地位,尤其适用于复杂零件和量产品的生产。
http://www.hfmaiqi.com