公差0.03
压制方式高压铸造
加工设备CNC加工中心
加工精度精加工
变形温度360
是否库存是
烧结温度305
加工材料铝合金,铜,不锈钢,钛合金
机加工零件是通过机械加工方法(如车削、铣削、钻削、磨削等)制造出来的零件,具有以下特点:
### 1. **高精度**
- 机加工零件能够达到的尺寸精度和几何精度,满足严格的公差要求。
- 表面粗糙度可以通过加工工艺控制,实现光滑或特定的表面质量。
### 2. **复杂形状**
- 机加工可以制造出复杂的几何形状,包括曲面、槽、孔、螺纹等。
- 通过数控机床(CNC)可以实现多轴加工,完成更复杂的零件设计。
### 3. **材料广泛**
- 机加工适用于多种材料,包括金属(如钢、铝、铜、钛合金等)、塑料、复合材料等。
- 不同材料可以通过调整加工参数来适应。
### 4. **一致性强**
- 批量生产时,机加工零件具有的一致性,适合大规模制造。
- 数控加工尤其能够保证零件的一致性和重复性。
### 5. **灵活性高**
- 机加工可以根据设计图纸快速调整工艺,适合小批量、多品种的生产。
- 数控编程可以灵活应对设计变更。
### 6. **表面处理多样化**
- 机加工后的零件可以进行多种表面处理,如电镀、喷涂、氧化、抛光等,以提高性能或美观性。
### 7. **成本与效率**
- 对于高精度或复杂零件,机加工成本较高,但能。
- 大批量生产时,通过优化工艺可以提率,降。
### 8. **适用性强**
- 机加工零件广泛应用于、汽车、设备、电子、模具制造等行业。
- 能够满足高强度、高耐磨性、耐腐蚀性等特殊要求。
### 9. **可加工硬质材料**
- 机加工可以处理硬度较高的材料,如淬火钢、硬质合金等,这是其他加工方法难以实现的。
### 10. **废料产生**
- 机加工属于减材制造,会产生一定的废料(如切屑),材料利用率相对较低。
总之,机加工零件以其高精度、复杂形状和广泛适用性,在现代制造业中占据重要地位。
绝缘材料加工具有以下几个显著特点:
1. **高绝缘性能要求**:绝缘材料的主要功能是阻止电流通过,因此加工过程中必须确保材料的绝缘性能不受损害。微小的缺陷或污染都可能导致绝缘性能下降,因此在加工过程中需要严格控制环境条件和操作规范。
2. **材料多样性**:绝缘材料种类繁多,包括塑料、橡胶、陶瓷、玻璃、云母、纤维等。不同材料的加工方法和工艺参数各不相同,需要根据具体材料的特性选择合适的加工工艺。
3. **加工精度要求高**:绝缘材料通常用于电子、电气设备中,对尺寸精度和表面质量要求较高。加工过程中需要采用高精度的设备和工艺,以确保成品的尺寸和形状符合设计要求。
4. **耐热性和耐化学性**:许多绝缘材料需要在高温或腐蚀性环境下工作,因此加工过程中需要考虑材料的耐热性和耐化学性。例如,某些材料在高温下容易变形或分解,加工时需要控制温度。
5. **机械性能要求**:绝缘材料不仅需要具有良好的绝缘性能,还需要具备一定的机械强度、韧性和耐磨性。加工过程中需要避免材料受到过大的机械应力,以防止开裂或变形。
6. **环保和安全要求**:绝缘材料加工过程中可能会产生粉尘、废气或有害物质,需要采取有效的环保措施,确保生产环境的安全和员工的健康。
7. **特殊加工工艺**:某些绝缘材料需要采用特殊的加工工艺,如注塑、挤出、压延、层压、涂覆等。这些工艺需要控制温度、压力和时间等参数,以确保材料的性能和质量。
8. **后处理要求**:绝缘材料加工后可能需要进行后处理,如热处理、表面处理或涂层处理,以进一步提高其性能或满足特定应用要求。
总之,绝缘材料加工是一个复杂且技术要求较高的过程,需要综合考虑材料特性、加工工艺、设备精度和环保安全等因素,以确保终产品的性能和质量。
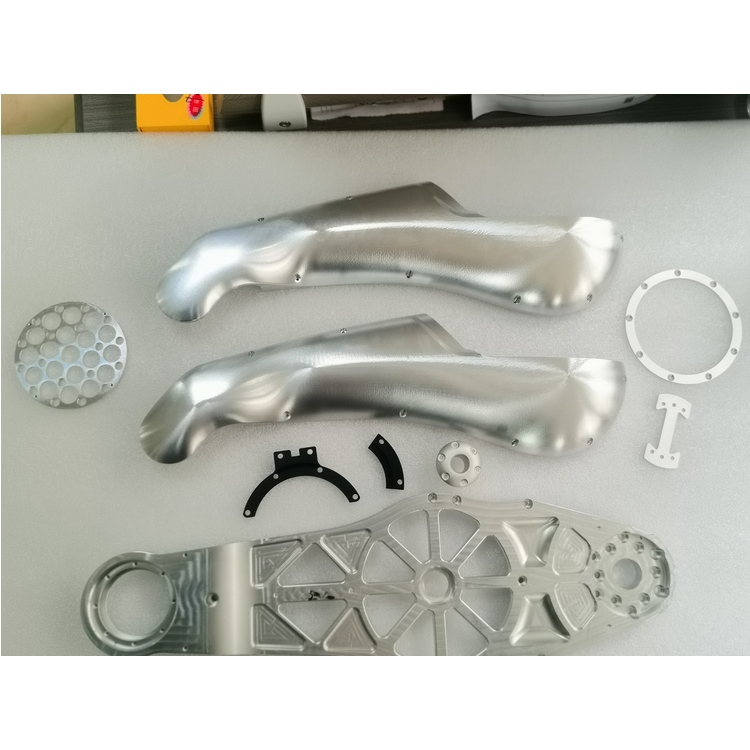
数控车床(Computer Numerical Control Lathe)是一种通过计算机程序控制加工过程的机床,具有高精度、率、高自动化等特点。以下是数控车床加工的主要特点:
### 1. **高精度与高重复性**
- 数控车床通过计算机程序控制的运动轨迹,能够实现微米级甚至更高精度的加工。
- 由于加工过程由程序控制,重复加工时能够保持高度一致,适合大批量生产。
### 2. **加工复杂形状能力强**
- 数控车床可以加工复杂的三维曲面、螺纹、锥面等形状,传统车床难以实现的复杂工件可以通过数控车床轻松完成。
- 通过多轴联动功能,可以实现更复杂的加工任务。
### 3. **自动化程度高**
- 数控车床可以自动完成从毛坯到成品的整个加工过程,减少了人工干预。
- 配备自动换刀装置(如刀塔)和自动上下料系统后,可以实现连续加工,进一步提率。
### 4. **加工效率高**
- 数控车床的切削速度和进给量可以控制,优化加工参数后能够显著提高加工效率。
- 减少了传统车床中手动调整和测量的时间,缩短了加工周期。
### 5. **灵活性高**
- 通过修改加工程序,可以快速适应不同工件的加工需求,特别适合多品种、小批量生产。
- 加工参数(如转速、进给量、切削深度等)可以根据工件材料和形状灵活调整。
### 6. **减少人为误差**
- 加工过程由程序控制,减少了操作人员的技术水平和经验对加工质量的影响。
- 降低了因人为操作失误导致的废品率。
### 7. **集成化与智能化**
- 现代数控车床通常配备智能化功能,如自动检测、磨损补偿、加工误差修正等,进一步提高了加工质量和效率。
- 可以与CAD/CAM系统无缝集成,实现从设计到加工的一体化流程。
### 8. **适用范围广**
- 数控车床可以加工材料,包括金属、塑料、复合材料等。
- 适用于多种行业,如、汽车制造、模具加工、器械等。
### 9. **减少工装夹具需求**
- 数控车床可以通过程序控制实现复杂形状的加工,减少了对工装夹具的依赖,降低了生产成本。
### 10. **环保与节能**
- 数控车床的加工过程更加,减少了材料浪费。
- 现代数控车床通常配备节能技术,降低了能源消耗。
### 总结
数控车床加工以其高精度、率、高自动化和灵活性的特点,在现代制造业中占据了重要地位。它不仅适用于大批量生产,也能满足多品种、小批量的加工需求,是提升生产效率和产品质量的重要工具。
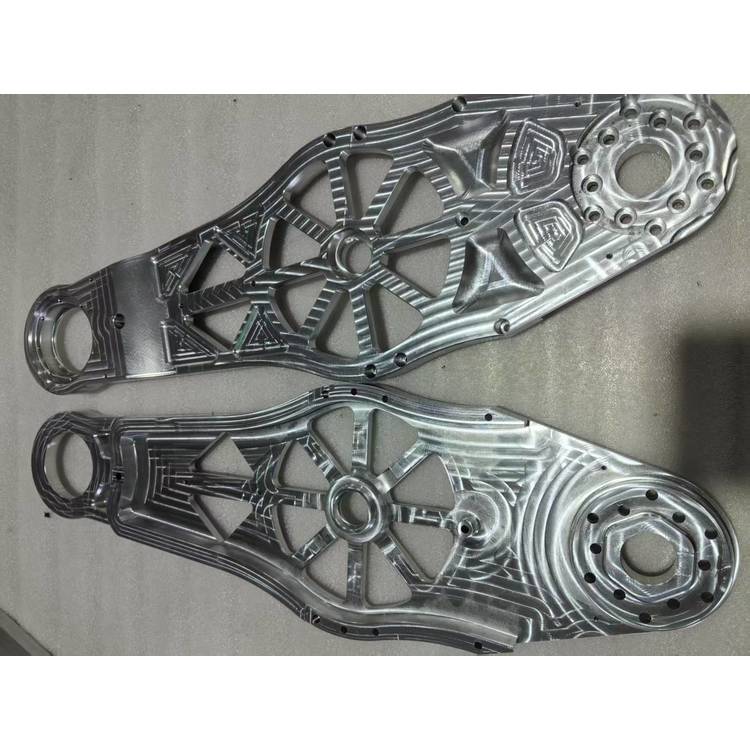
陶瓷焊接加工是一种用于连接陶瓷材料的特殊工艺,具有以下特点:
### 1. **高难度性**
- 陶瓷材料通常具有高硬度、脆性和低延展性,焊接过程中容易产生裂纹或断裂,因此对工艺要求高。
### 2. **高温需求**
- 陶瓷的熔点通常较高,焊接时需要高温环境,有时甚至需要借助激光、电子束等技术来实现。
### 3. **特殊焊接方法**
- 常用的陶瓷焊接方法包括:
- **扩散焊接**:通过高温和压力使陶瓷表面原子扩散形成连接。
- **活性金属钎焊**:使用活性钎料(如钛、锆等)改善陶瓷与金属或陶瓷之间的润湿性。
- **激光焊接**:利用高能激光束实现局部加热和熔化。
- **超声波焊接**:通过超声波振动产生热量实现连接。
### 4. **材料匹配性要求高**
- 陶瓷与金属或其他陶瓷的焊接需要材料的热膨胀系数、化学相容性等性能相匹配,否则容易产生应力或失效。
### 5. **接头质量关键**
- 焊接接头的强度、气密性和耐腐蚀性是衡量焊接质量的重要指标,需要严格控制工艺参数。
### 6. **应用领域广泛**
- 陶瓷焊接加工广泛应用于、电子、器械、能源等领域,如陶瓷基复合材料、高温传感器、燃料电池等。
### 7. **设备和技术要求高**
- 需要高精度的设备和的技术支持,如真空环境、的温度控制和压力控制等。
### 8. **成本较高**
- 由于工艺复杂、设备昂贵,陶瓷焊接加工的成本通常较高。
总之,陶瓷焊接加工是一项技术密集型工艺,需要综合考虑材料特性、工艺方法和应用需求,以实现量的连接效果。
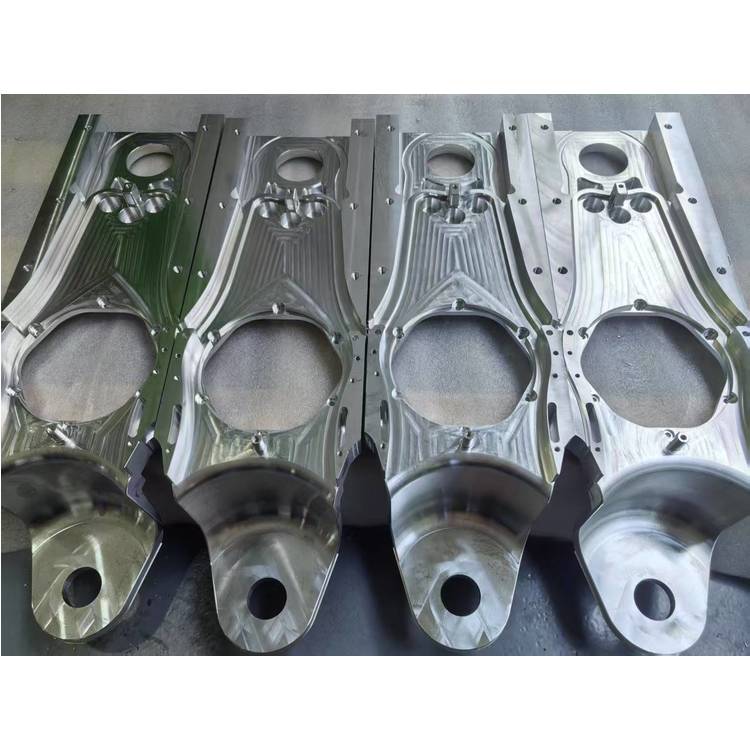
机械零件加工的特点主要包括以下几个方面:
### 1. **高精度要求**
- 机械零件加工通常对尺寸精度、形状精度和位置精度有严格要求,以确保零件在装配和使用过程中能够达到预期的性能。
- 加工精度通常以微米(μm)为单位,某些高精度零件甚至要求达到纳米级别。
### 2. **多样化的加工方法**
- 机械零件加工涉及多种加工方法,如车削、铣削、磨削、钻削、镗削、拉削、冲压、铸造、锻造等。
- 根据零件的材料、形状和精度要求,选择合适的加工工艺。
### 3. **材料种类广泛**
- 机械零件加工涉及的材料种类繁多,包括金属(如钢、铝、铜、钛等)、合金、塑料、陶瓷、复合材料等。
- 不同材料的加工性能和工艺参数差异较大,需要根据材料特性调整加工方法。
### 4. **复杂的几何形状**
- 机械零件的形状多样,包括轴类、盘类、箱体类、异形件等。
- 加工过程中需要处理复杂的几何特征,如曲面、螺纹、孔、槽、齿轮等。
### 5. **批量生产与单件生产并存**
- 机械零件加工既包括大批量生产(如汽车零部件、标准件),也包括单件或小批量生产(如定制设备、模具)。
- 批量生产通常采用自动化设备和流水线作业,而单件生产则更注重灵活性和定制化。
### 6. **设备与工具的高要求**
- 机械零件加工需要高精度、率的加工设备,如数控机床(CNC)、加工中心、磨床等。
- 加工的选择和磨损控制对加工质量和效率有重要影响。
### 7. **工艺链长**
- 机械零件的加工通常需要经过多道工序,如毛坯制备、粗加工、半精加工、精加工、热处理、表面处理等。
- 各工序之间需要紧密配合,以确保终零件的质量和性能。
### 8. **严格的质量控制**
- 机械零件加工过程中需要进行严格的质量检测,包括尺寸测量、表面粗糙度检测、硬度测试、无损检测等。
- 质量控制贯穿于整个加工过程,以确保零件符合设计要求和标准。
### 9. **成本与效率的平衡**
- 机械零件加工需要在的前提下,尽可能降和提率。
- 通过优化工艺、采用设备和技术、提高自动化程度等方式,实现成本与效率的平衡。
### 10. **环境与安全要求**
- 机械零件加工过程中会产生切屑、粉尘、噪音、振动等,需要采取环保措施,如切屑回收、除尘、降噪等。
- 操作人员需要遵守安全操作规程,佩戴防护装备,以防止事故的发生。
### 11. **技术更新快**
- 机械零件加工技术不断发展,如数控技术、增材制造(3D打印)、智能制造、绿色制造等新技术的应用,提高了加工精度、效率和环保性。
- 企业需要不新设备和技术,以适应市场需求和技术进步。
### 12. **定制化与标准化结合**
- 机械零件加工既需要满足标准化生产的要求,也需要根据客户需求进行定制化设计。
- 标准化零件可以通过大规模生产降,而定制化零件则能够满足特定应用场景的需求。
总之,机械零件加工是一个复杂且技术要求高的领域,涉及多方面的知识和技能,需要综合考虑材料、工艺、设备、质量、成本等因素,以实现、量的加工目标。
铝合金件精加工的特点主要包括以下几个方面:
### 1. **材料特性**
- **轻质高强**:铝合金密度低,但强度较高,适合制造轻量化零件。
- **导热性好**:铝合金的导热性能,加工时散热快,有助于减少热变形。
- **易加工性**:铝合金硬度较低,切削性能好,易于进行精加工。
### 2. **加工工艺**
- **高精度**:精加工要求尺寸精度高,表面光洁度好,通常使用数控机床(CNC)进行加工。
- **选择**:铝合金加工通常使用硬质合金或金刚石,以减少磨损和提高加工质量。
- **冷却润滑**:加工过程中使用冷却液或润滑剂,以防止材料粘刀和减少热变形。
### 3. **表面处理**
- **阳氧化**:提高表面硬度和耐腐蚀性,同时可以着色,增加美观性。
- **抛光**:通过机械或化学抛光,获得高光泽的表面。
- **涂层**:如电镀、喷涂等,增强表面性能或提供装饰效果。
### 4. **质量控制**
- **尺寸检测**:使用精密测量工具(如三坐标测量机)确保尺寸精度。
- **表面检测**:通过显微镜或表面粗糙度仪检测表面质量。
- **材料检验**:确保铝合金材料的化学成分和机械性能符合要求。
### 5. **应用领域**
- ****:铝合金件在领域应用广泛,因其轻质高强的特性。
- **汽车工业**:用于制造车身部件、发动机零件等,以减轻整车重量。
- **电子产品**:用于制造外壳、散热片等,具有良好的导热性和美观性。
### 6. **环保与成本**
- **可回收性**:铝合金可回收再利用,。
- **成本效益**:虽然铝合金材料成本较高,但其加工性能和轻量化优势使其在长期使用中具有成本效益。
### 7. **挑战与解决方案**
- **热变形**:通过优化加工参数和使用冷却液减少热变形。
- **磨损**:选择合适的材料和涂层,延长寿命。
- **表面缺陷**:通过精细的工艺控制和后续处理,减少表面缺陷。
总的来说,铝合金件精加工具有高精度、率和高表面质量的特点,广泛应用于多个高要求的工业领域。
http://www.hfmaiqi.com